Milling is a crucial part of making things with precision in modern manufacturing. It’s like the architectural backbone, helping create detailed parts accurately. What is milling? Simply put, milling is about removing material from an object using special tools to make different shapes. This article explores the world of milling, looking at its history, how it has evolved, and why it’s important today.
Significance of Milling Machines in Modern Manufacturing
In the world of advanced manufacturing, milling machines are like technological heroes. They’ve changed how we make things, especially in industries like aerospace and healthcare. These machines are not just good at creating detailed designs; they also drive innovation, pushing the limits of what we can achieve with precision engineering.
Purpose of the Article: Unveiling the Latest Technological Marvels in Milling
This article aims to uncover the newest and coolest technologies in milling machines. As manufacturing keeps changing, so do the tools and methods we use. We want to explore the latest advancements, smart strategies, and how milling is being used in real life. Our goal is to give you a clear picture of how these amazing technologies are shaping the future of making things with extreme precision. Come along as we reveal the most exciting advancements in the world of milling.
Milling is like using a sculptor’s tool in manufacturing. It’s a way of carefully taking away material from an object, using special tools to shape it precisely. In other words, milling is a fundamental machining process that involves shaping materials into precise forms.
Definition of Milling:
At its core, milling is akin to a sculptor carving away excess material to reveal a desired shape. It’s a subtractive manufacturing process that uses specialized tools to cut, shape, and create intricate components.
How Milling Works:
- Tool and Workpiece Interaction: Milling machines use rotating cutting tools, such as end mills or face mills, to remove material from a workpiece.
- Axes Movement: The workpiece and cutting tool can move along different axes (X, Y, Z), allowing for versatile shaping and detailing.
Alt text: How milling works
Types of Milling Machines:
- Vertical Mills: The spindle moves up and down, ideal for tasks like face milling.
- Horizontal Mills: The spindle moves side to side, providing stability and effective chip removal.
- Specialized Mills: Bed mills, turret mills, knee mills, and gantry mills cater to specific applications.
Understanding these fundamental aspects provides a solid foundation for appreciating the role of milling in modern manufacturing.
Importance of Milling in Precision Engineering
Why is CNC milling so important for making things with extreme accuracy? Milling provides distinct benefits when it comes to precision engineering, namely:
- Crafting Intricate Components: Milling is crucial for creating precise and detailed parts used in various industries.
- High-Level Accuracy: The ability to achieve tight tolerances makes milling indispensable for precision engineering.
But first, in order to better understand what is milling, and its impact on the manufacturing industry let’s take a look at some of the technological marvels in CNC milling.
High-Speed Machining (HSM) and Its Impact
Ever wondered how machines can be faster without losing precision? High-Speed Machining (HSM) is like the superhero speeding up CNC milling. By turning up the speed and precision, HSM reduces waiting times and makes surfaces smoother. Real-world examples showcase how HSM is transforming the efficiency of CNC milling, making it faster and better.
Trochoidal Milling: Smart Moves for Better Efficiency
Trochoidal Milling, also known as adaptive techniques, is like the clever dancer in the CNC milling world. By using circular paths, Trochoidal Milling makes tools last longer and reduces the force needed, making the milling process super-efficient. Practical examples reveal how this technique is changing the game, making CNC milling smarter and more effective.
Alt text: Slicing and trochoidal milling
Advanced Toolpath Optimization Strategies
Imagine planning the best route for a road trip. Toolpath optimization is like the GPS for CNC milling machines. By avoiding sharp turns and ensuring a smooth journey, toolpath optimization enhances efficiency and keeps tools in great shape. This smart planning contributes to better outcomes in CNC milling. The impact of advanced toolpath optimization, making the milling process more efficient and precise is undeniable.
Progress in milling technology introduces advanced features to improve efficiency and accuracy. Explore these notable innovations:
Intelligent Cooling Methods: Through-Spindle Coolant, Mist Cooling
In the precision-focused realm of milling, combating heat generation is a critical concern. Innovative cooling methods are essential for peak milling machine performance, addressing the impact of high temperatures on tooling and machining results.
- Through-Spindle Coolant: This inventive technique delivers coolant directly to the cutting tool through the spindle, efficiently managing heat at the tool-workpiece contact point. This precision coolant delivery system prevents tool overheating and significantly extends tool lifespan, ensuring optimal operating conditions.
- Mist Cooling: Another advanced method involves applying a fine mist of coolant around the cutting area during milling. This mist acts as a protective shield, reducing temperatures and mitigating the risk of overheating. Besides temperature regulation, mist cooling aids in chip removal, enhancing overall milling efficiency.
These cooling innovations strategically address challenges linked to overheating in milling processes. By maintaining a controlled temperature environment, these methods are pivotal in sustaining CNC milling precision and efficiency, leading to superior machining outcomes and prolonged tool life.
Precision Management: Techniques for Controlling Tool Interaction
Achieving top precision in milling is an art that relies on advanced techniques for managing the delicate dance between cutting tools and workpieces. Precision management is crucial, ensuring each movement contributes to flawless, highly accurate machined components.
- Constant Engagement Toolpaths: This sophisticated technique involves carefully planning toolpaths to maintain a consistent load on the cutting tool throughout the machining process. Critical for intricate designs, it enhances surface finishes, contributing to the overall precision of the final product.
- Runout Control: Minimizing tool wobbling, or runout, is vital for overall milling accuracy. Precision management employs control measures to minimize runout, ensuring the cutting tool moves with minimal deviation. This meticulous approach is a cornerstone for achieving the highest level of precision, especially in intricate geometries and tight tolerances.
As CNC milling evolves, refining these techniques is increasingly critical for meeting the demands of modern manufacturing, where precision is not just a goal but an absolute necessity.
Innovations in Workholding: Vacuum Chucks, Magnetic Clamping
Ensuring stability in the milling process is of paramount importance, and the role of innovative workholding solutions cannot be overstated:
- Vacuum Chucks: These cutting-edge workholding solutions leverage suction to securely grip the workpiece in place. This method is versatile, suitable for a wide range of materials. By utilizing vacuum chucks, the workpiece is effectively held during milling, contributing to stable and accurate machining.
- Magnetic Clamping: Employing magnetic forces, this technique is specifically designed for securing ferrous materials. Magnetic clamping provides a robust hold, ensuring stability throughout the milling operation. Particularly beneficial when working with materials prone to movement, it establishes a reliable foundation for precision machining.
These advancements in workholding not only address the challenge of workpiece stability but also lay the groundwork for accurate milling, especially when dealing with intricate or heavy workpieces. As milling technology continues to advance, these features underscore a commitment to achieving exceptional precision, efficiency, and adaptability in the machining process.
Aerospace: Transforming the Sky with CNC Milling
Imagine the machines that help build airplanes and rockets, making them safer and more efficient. That’s where CNC milling comes in. CNC milling is like a superhero in aerospace engineering. It helps create important parts for aircraft, like powerful engines and lightweight structures. There are real examples and cool innovations where CNC milling is crucial for making aircraft better and safer.
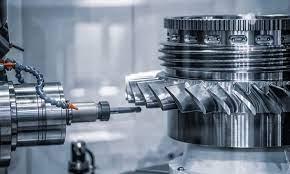
Alt text: precision milling aerospace parts
Healthcare: Making Precise Medical Parts
Precision is super important in healthcare, especially when making things like artificial joints and custom-made medical devices. CNC milling is like a champion in healthcare, making sure medical parts are just right. CNC milling helps create intricate medical components, improving patient care with precise and personalized devices. Real-life stories and examples show how technology, like CNC milling, is making a big difference in the medical world.
Automotive: CNC Milling Drives Innovation
When you think about cool and new things happening with cars, CNC milling is often behind the scenes, making it all possible. CNC milling is like the wizard of innovation in the automotive world. It helps shape tricky car parts with amazing accuracy and adds to the design and features of vehicles. Real stories and the latest tech advancements reveal that CNC milling is a key player in making cars better and steering the future of transportation.
Current Challenges in CNC Milling Technology
Despite the strides in CNC milling, certain challenges persist:
- Complex Programming: The intricacies of programming CNC machines pose challenges, requiring skilled operators.
- Tool Wear and Breakage: Continuous milling operations lead to wear and breakage of cutting tools, impacting efficiency.
- Cost of High-End Equipment: Acquiring and maintaining advanced CNC milling equipment can be costly for smaller manufacturers.
Navigating these challenges is essential for maximizing the benefits of CNC milling technology.
Anticipated Technological Advancements
The future holds promising advancements in CNC milling technology:
- Artificial Intelligence Integration: AI-driven systems may optimize milling processes, improving efficiency and reducing errors.
- Enhanced Materials and Coatings: Innovations in tool materials and coatings could extend tool life and elevate machining capabilities.
- Real-time Monitoring: Advanced monitoring systems may enable real-time assessment of milling processes, enhancing precision.
These anticipated advancements aim to address current limitations and push the boundaries of what CNC milling can achieve.
Shaping the Future of Milling: Industry Predictions
Experts foresee several trends shaping the future of CNC milling:
- Increased Automation: Growing integration of automation in milling processes, leading to improved productivity.
- Customization and Small-Batch Production: A shift towards more customized, small-batch production to meet diverse consumer demands.
- Sustainable Practices: Emphasis on eco-friendly milling practices, incorporating recyclable materials and energy-efficient technologies.
These predictions underscore the industry’s commitment to innovation, sustainability, and meeting the evolving needs of modern manufacturing. As CNC milling continues to evolve, overcoming challenges and embracing future trends will be crucial for staying at the forefront of precision engineering.
In the intricate world of milling, where precision is paramount and innovation is constant, this exploration has delved into the core of what makes manufacturing truly remarkable. Milling, the sculptor’s tool in modern manufacturing, stands as the architectural backbone, shaping detailed components with precision. The understanding of milling basics, its role in precision engineering, and the exploration of CNC milling’s cutting-edge features highlight the commitment to achieving excellence in the machining process.
Q1: What is the primary purpose of milling in modern manufacturing?
Answer: Milling in modern manufacturing serves as a fundamental machining process aimed at shaping materials into precise forms. It involves the removal of material from an object using specialized tools, contributing to the creation of intricate components with high-level accuracy.
Q2: How does CNC milling contribute to innovation in industries like aerospace and healthcare?
Answer: CNC milling plays a pivotal role in innovation by providing a versatile and precise method for crafting components. In aerospace, it helps create essential parts for aircraft, ensuring safety and efficiency. In healthcare, CNC milling is instrumental in producing precise medical components, such as artificial joints, contributing to advancements in patient care.