As automation expands across industries, collaborative robots, or “cobots,” are emerging as essential tools for tasks that require precision and safe human-robot interaction. Designed to work alongside humans in a shared space, cobots are revolutionizing industries by combining sophisticated technology with user-friendly interfaces.
Core Structure of a Cobot
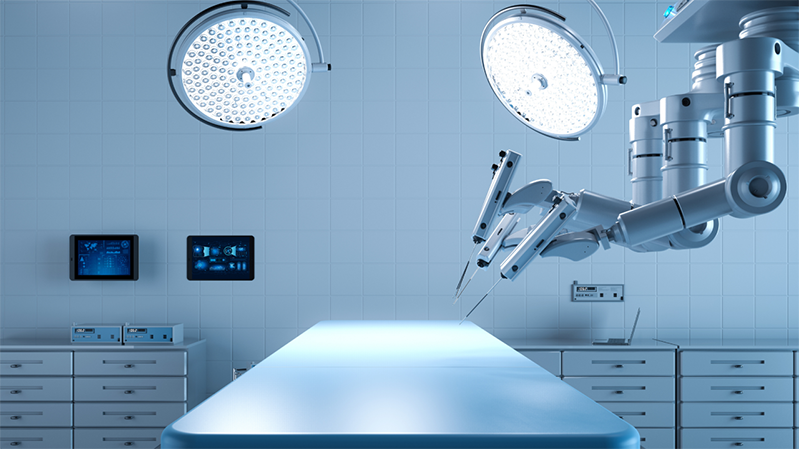
The frame and joints form the skeletal structure of a cobot, giving it shape, stability, and flexibility. Typically crafted from lightweight materials like aluminum alloys or composites, the frame supports the cobot’s structure without compromising mobility.
Cobots are often built with multiple joints, each allowing a specific type of motion, such as rotational or linear movement. These joints create degrees of freedom, enabling the cobot to replicate human-like movements or make adjustments based on task requirements. Flexible joints allow cobots to operate in various orientations and spaces, making them suitable for dynamic tasks across industries like manufacturing, warehousing, and healthcare.
Actuators
Actuators are essential components that convert energy into movement, enabling cobots to perform precise tasks. Most cobots use electric actuators because of their fine-tuned control and energy efficiency, which is ideal in collaborative settings where power and responsiveness are critical.
Electric actuators allow cobots to carry out subtle, controlled movements. For instance, in tasks like assembly or inspection, the ability to fine-tune movement can make the difference between success and damage. In environments where precise pressure control is needed, electric actuators excel by offering accurate, programmable movements.
Sensors – The Cobot’s Sense of Environment and Safety
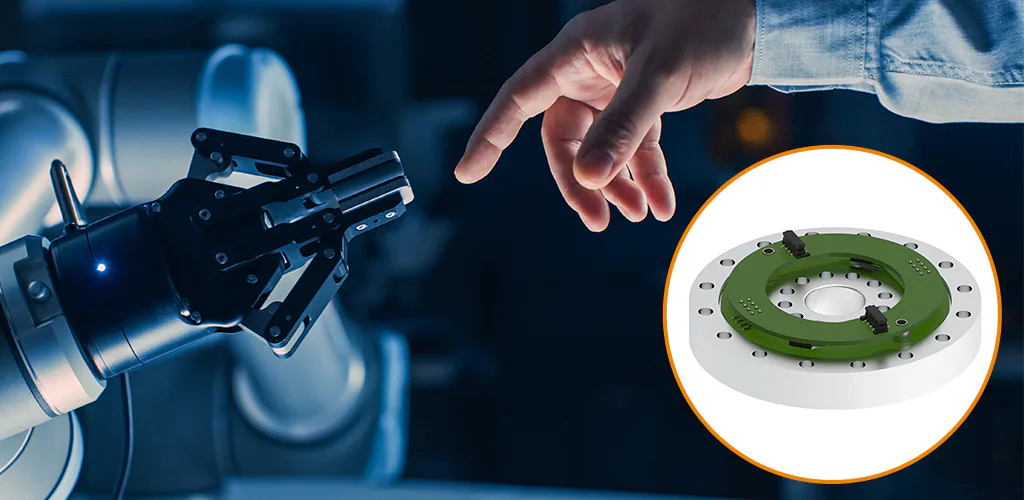
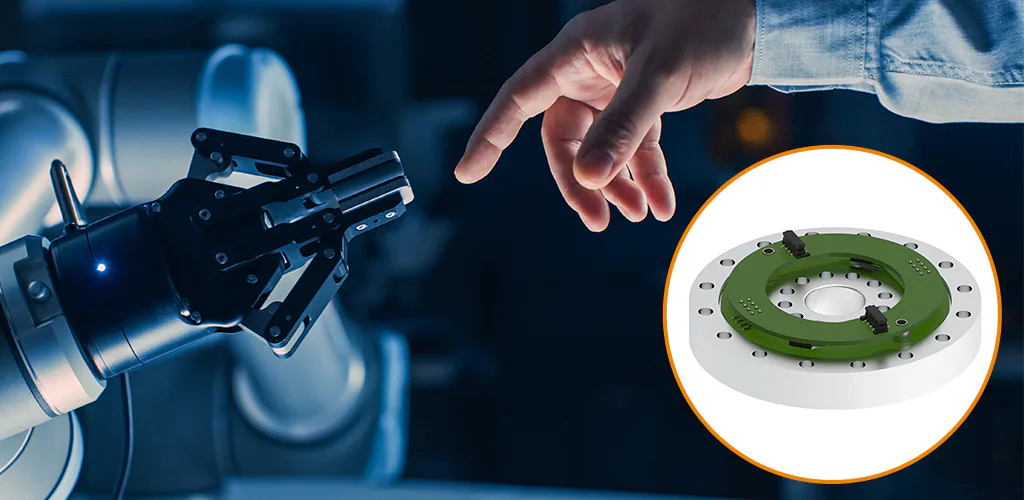
Sensors are the “senses” of a cobot, allowing it to perceive its surroundings, detect obstacles, and interact safely with humans and objects. Sensor data is continuously gathered and processed to enable real-time adaptability, which is crucial in fast-paced environments where conditions may change frequently.
Cobots rely on a variety of sensors, each serving a unique purpose:
- Proximity Sensors: These sensors detect the presence of objects or people near the cobot. By measuring the distance between the cobot and obstacles, proximity sensors help prevent collisions and facilitate safe human-robot interaction. This is particularly important when cobots work in close quarters with people.
- Force/Torque Sensors: Force sensors measure the amount of force or torque exerted during tasks, allowing cobots to apply the right amount of pressure. This feature is critical in applications like assembly, where over-tightening could damage parts, or in handling fragile items, where excessive force might lead to breakage.
- Vision Systems: Vision systems, often using advanced 3D laser line profile sensors like Gocator, provide cobots with the ability to “see.” Equipped with cameras and image sensors, vision systems help cobots identify objects, patterns, and even imperfections, making them invaluable in quality control and sorting tasks.
- Temperature and Environmental Sensors: These sensors help monitor the cobot’s operating environment, ensuring that it doesn’t overheat or encounter hazardous conditions. In temperature-sensitive applications, these sensors allow the cobot to adjust or pause its operations to prevent damage.
- Pressure Sensors: Pressure sensors allow cobots to handle delicate materials with precision. They are particularly useful in industries like pharmaceuticals or food handling, where precision and care are paramount.
Control Systems – The Cobot’s “Brain”
The CPU serves as the cobot’s central processing unit, orchestrating its movements, processing sensor inputs, and ensuring that the cobot performs tasks accurately and efficiently. With advancements in processing speed, modern cobots can handle complex tasks and respond quickly to changes in their environment, making them valuable in fast-paced or unpredictable settings.
Software and Algorithms
Cobots rely on advanced software and algorithms that govern their actions. These control algorithms enable cobots to carry out precise movements, recognize objects, and adapt to new tasks without extensive reprogramming. Algorithms like adaptive learning allow cobots to “learn” from previous tasks, enhancing their effectiveness over time.
Machine learning, a type of artificial intelligence, is increasingly being integrated into cobots. This enables cobots to adjust their performance based on real-time data, optimizing their workflow and improving efficiency in the long run.
Human-Machine Interface (HMI)
An intuitive Human-Machine Interface (HMI) is essential for cobots, allowing human operators to control, monitor, and program them. Common HMI devices include teach pendants, touchscreens, and even voice-activated controls. These interfaces simplify the cobot programming process, making it easier for operators to modify instructions, troubleshoot issues, or monitor performance.
End Effectors – Tools for Task Execution
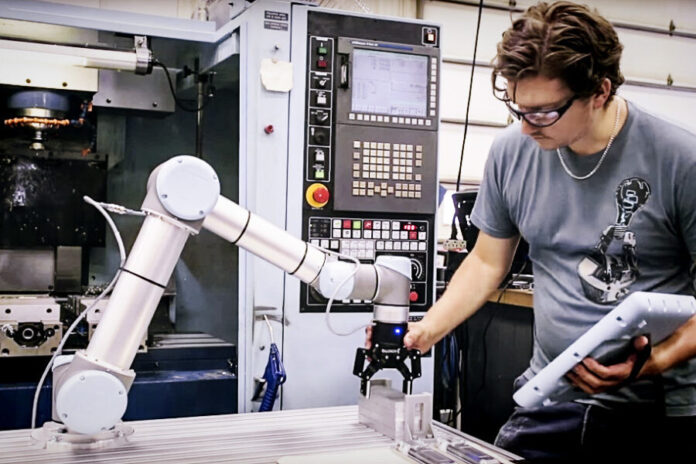
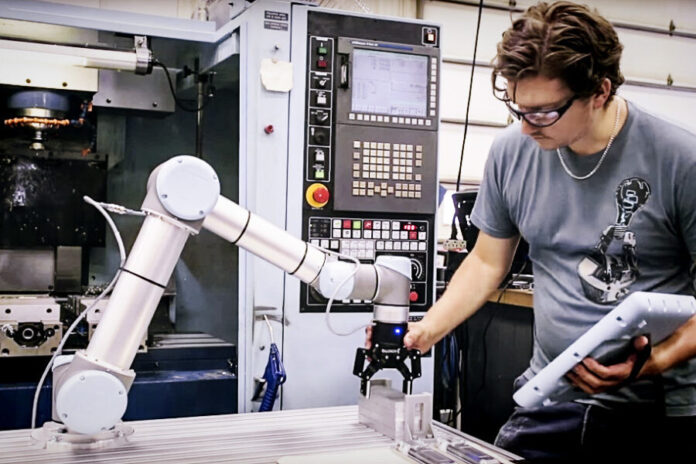
End effectors are the cobot’s “hands,” performing the physical actions required to complete tasks. They are the tools that come in direct contact with the cobot’s work environment, allowing it to pick up, manipulate, or interact with objects.
- Grippers: Commonly used in material handling, grippers allow cobots to grasp, hold, and release objects. They come in various types, including soft grippers that handle delicate items like food or medical supplies without causing damage.
- Welding Tools: Used in manufacturing applications, welding end effectors enable cobots to perform precise welding tasks, reducing human exposure to hazardous environments.
- Suction Cups and Vacuum Systems: Ideal for tasks involving smooth or fragile items, suction systems allow cobots to lift and move items without causing scratches or deformation.
- Specialized Tools: Cobots can also be equipped with custom tools for specific applications, such as painting or screwing. These specialized end effectors enable cobots to complete tasks that require specialized handling or precision.
One of the advantages of cobots is the ability to switch between different end effectors, making them highly versatile. With a quick-change system, operators can swap tools in seconds, allowing the cobot to transition between tasks seamlessly and increasing overall productivity.
Conclusion
The anatomy of a cobot reveals a highly sophisticated machine, designed with precision, adaptability, and safety in mind. Each part, from the frame and joints to sensors and control systems, plays a crucial role in enabling cobots to perform tasks efficiently in a collaborative environment. As cobot technology advances, we can expect to see even greater flexibility, efficiency, and application diversity, solidifying cobots’ role in the future of automation.