Shot blasting plays a crucial role in industrial surface finishing, helping to clean, strengthen, and prepare surfaces for further processing. Whether it is removing rust, scale, or contaminants from metal surfaces or creating the right texture for coatings and paint adhesion, shot blasting is a highly effective method used across various industries.
The choice of shot blasting material is a key factor in determining the efficiency, quality, and cost-effectiveness of the process. This is why businesses often rely on shot blasting material suppliers to provide high-quality abrasives tailored to their specific needs.
Key Points:
- Shot blasting removes contaminants and improves surface adhesion.
- Different industries rely on shot blasting for cleaning, deburring, and strengthening surfaces.
- The choice of abrasive material affects process efficiency and final finish quality.
- Suppliers play a key role in ensuring high-quality shot blasting materials.
- Proper material selection influences cost-effectiveness and sustainability.
Understanding Shot Blasting and Its Applications
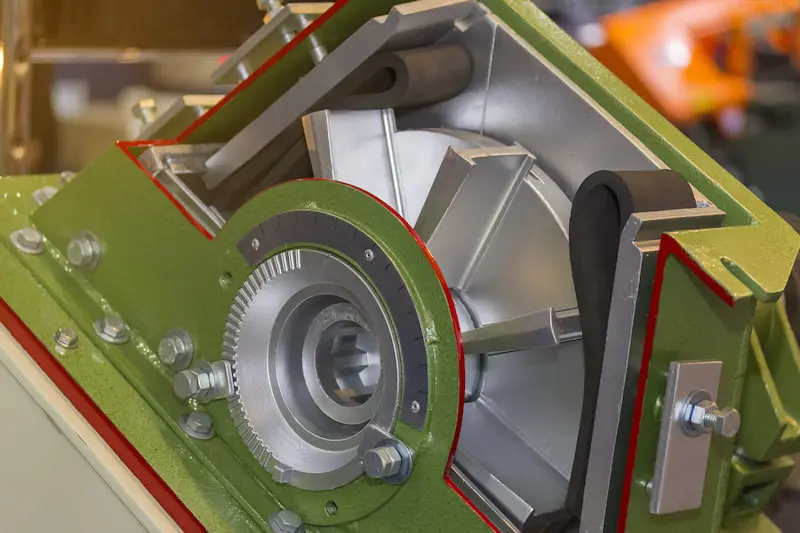
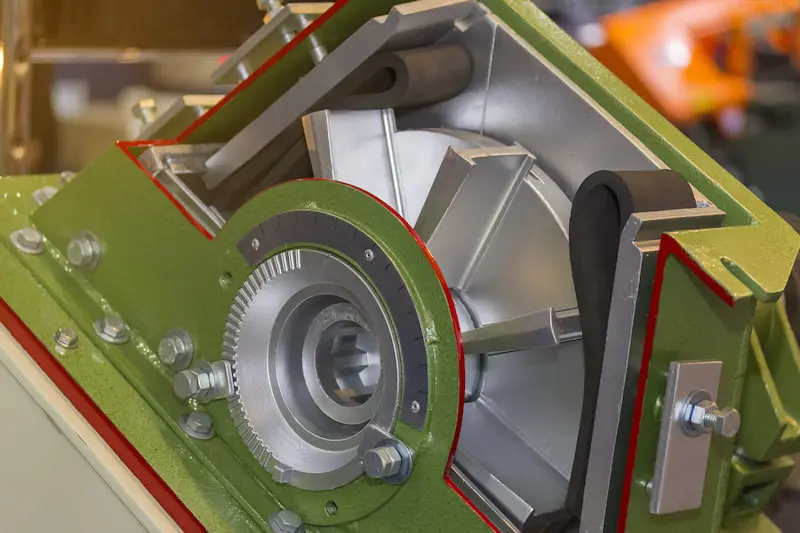
Shot blasting is a mechanical process where abrasive materials are propelled at high speeds against a surface to remove impurities, improve texture, or enhance durability. This method is widely used in industries such as automotive, construction, aerospace, and manufacturing. It is particularly effective for:
- Surface Preparation – Ensuring better adhesion for coatings, paints, and finishes.
- Cleaning – Removing rust, scale, and old coatings from metal surfaces.
- Deburring – Eliminating sharp edges or burrs from machined components.
- Strengthening (Peening) – Improving fatigue resistance by inducing compressive stress on metal surfaces.
Types of Shot Blasting Materials
The effectiveness of the shot blasting process depends on selecting the right type of abrasive material. Some of the most common shot blasting materials include:
- Steel Shot and Grit – These are commonly used for heavy-duty applications such as descaling, deburring, and surface hardening. Steel abrasives are durable, reusable, and provide a uniform finish.
- Aluminium Oxide – A sharp and hard abrasive ideal for aggressive cleaning and etching of surfaces. It is frequently used in the aerospace and automotive sectors.
- Glass Beads – Best suited for achieving a smooth, satin finish, glass beads are widely used for cosmetic surface treatments and delicate materials.
- Garnet – A natural and eco-friendly abrasive, garnet is often chosen for its ability to clean surfaces without embedding particles into the material.
- Plastic Media – Used for gentle stripping applications, plastic media prevents damage to delicate substrates such as fibreglass and aluminium.
The Role of Hardness in Shot Blasting Efficiency
Abrasive hardness plays a critical role in the shot blasting process. Harder abrasives provide aggressive material removal, making them suitable for heavy-duty applications like rust and scale removal. Softer abrasives, on the other hand, offer a controlled approach that preserves surface integrity while achieving a smooth finish. Choosing the right hardness level depends on the material being treated and the desired surface outcome.
Factors Influencing Hardness Selection:
- The toughness of the material being blasted.
- The level of surface roughness required.
- The need for reusability and cost-effectiveness.
- The presence of coatings or embedded contaminants.
The Importance of Choosing the Right Shot Blasting Material Suppliers
Reliable shot blasting material suppliers are essential to ensuring that businesses receive high-quality abrasives that meet industry standards. Factors to consider when selecting a supplier include:
- Material Quality – Ensuring consistency, hardness, and durability of the abrasives.
- Availability and Supply Chain Efficiency – Reliable suppliers help prevent downtime by maintaining a steady supply of materials.
- Environmental Considerations – Many industries are shifting towards eco-friendly abrasives, making it important to choose suppliers who offer sustainable options.
- Technical Support – The right supplier provides guidance on selecting the most suitable abrasive for specific applications.
Sustainability in Shot Blasting Materials
Environmental concerns have led to increased demand for sustainable shot blasting materials. Many industries are moving towards eco-friendly alternatives that reduce waste and minimize environmental impact. Choosing abrasives that can be recycled multiple times reduces costs while maintaining efficiency.
Sustainable Shot Blasting Options:
- Garnet – A natural mineral that can be reused without producing hazardous waste.
- Glass Beads – Made from recycled glass, offering an environmentally friendly alternative.
- Plastic Media – Reduces the risk of material contamination and is biodegradable.
- Steel Grit – Highly durable and reusable, leading to minimal waste production.
Shot Blasting Equipment and Process Optimization
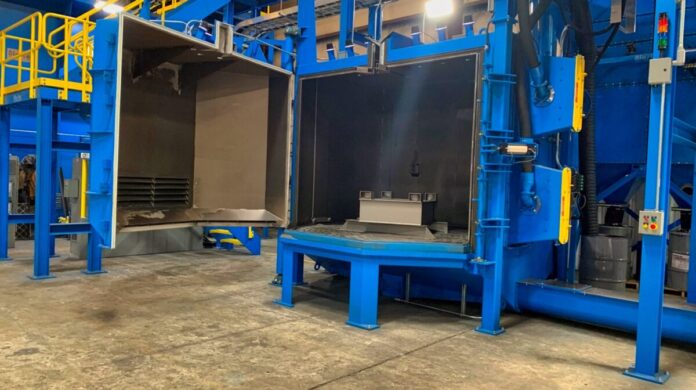
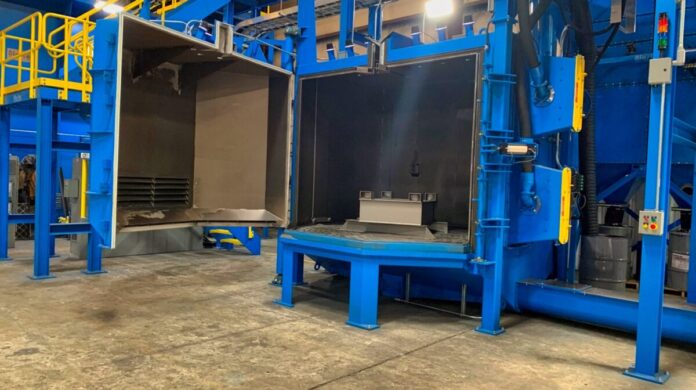
The efficiency of shot blasting depends on both the abrasive material and the equipment used. Optimized equipment settings ensure consistent performance, reduce abrasive consumption, and improve final surface quality. Operators must carefully adjust pressure, speed, and nozzle distance to achieve the desired results.
Best Practices for Optimization:
- Regularly inspect blasting machines for wear and tear.
- Adjust nozzle angles to control impact intensity.
- Use appropriate pressure settings for different abrasives.
- Ensure proper ventilation to prevent dust accumulation.
Cost Considerations in Shot Blasting Material Selection
The selection of shot blasting materials impacts operational costs significantly. Businesses must balance cost-effectiveness with efficiency to ensure the best results without excessive expenses. Some abrasives provide long-term value due to their durability and reusability, reducing the frequency of replacement.
Key Cost Factors to Consider
1. Material Longevity – Reusable Abrasives Reduce Costs Over Time
Choosing abrasives that can be reused multiple times lowers long-term expenses. Single-use materials may seem cheaper upfront, but they require frequent replenishment. Durable options like steel grit or aluminum oxide provide extended usability, making them a cost-effective choice for high-volume operations.
2. Processing Speed – Faster Cleaning Reduces Labor and Energy Expenses
Abrasives with higher efficiency reduce the time needed for surface preparation. Faster processing means lower labor costs and reduced energy consumption. Materials like garnet and silicon carbide offer aggressive cutting action, making them ideal for quick and effective cleaning.
3. Waste Management – Environmentally Friendly Options Can Lower Disposal Costs
Disposing of spent abrasives can be expensive, especially when dealing with hazardous waste. Eco-friendly choices, such as water-soluble or recyclable media, help cut down on disposal fees. Some facilities even recover and recycle used abrasives, minimizing waste and overall operating costs.
4. Supplier Pricing – Reliable Supply Chains Affect Expenses
Buying in bulk often leads to significant savings, but supply consistency matters just as much. A supplier with a strong distribution network ensures steady availability, preventing downtime and last-minute premium purchases. Comparing prices from multiple vendors helps secure the best deal without sacrificing quality.
Conclusion
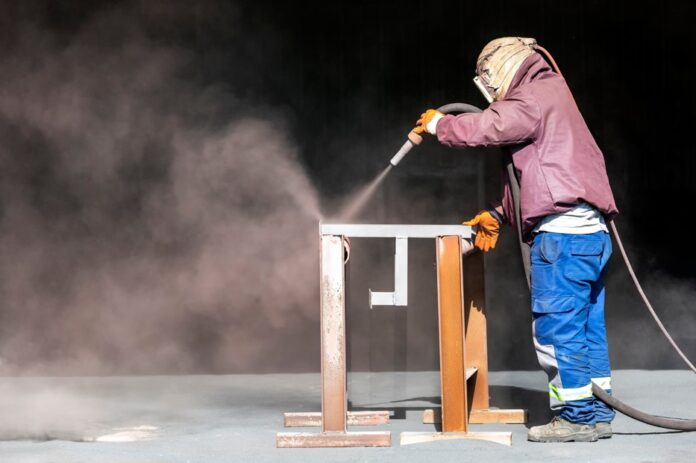
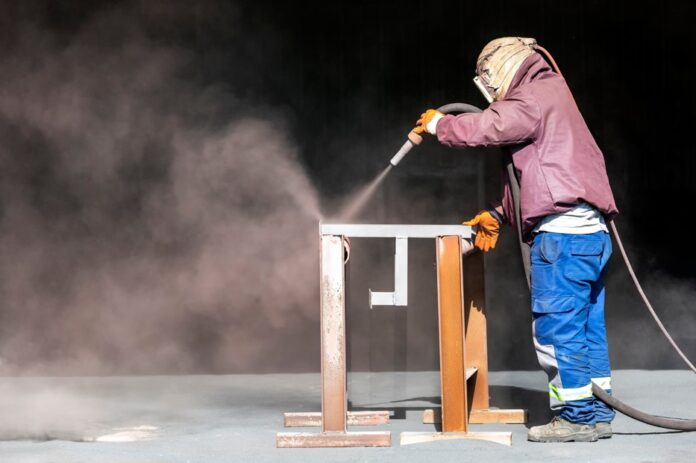
Shot blasting is a vital process in industrial surface finishing, and the choice of abrasive material has a direct impact on the quality and efficiency of the process. Whether working with steel, aluminium oxide, or glass beads, partnering with trusted shot blasting material suppliers ensures businesses achieve the best results for their surface preparation and finishing needs. Optimizing shot blasting operations by selecting the right abrasives and equipment enhances productivity and cost savings. Industries shifting towards sustainable solutions can benefit from eco-friendly materials that offer both performance and environmental advantages.